Concurrent vs Serial Multiscale Modelling of Intelligent MFC Composite CFRP-PZT (A general concept)
For trainings and files, Please write me an email or reach out to me via:
Email: arsalanmuhammadahmad@yahoo.com
Whatsaap# +92-315-9779633
Website# https://arsalanmaa.com/design-simulation/
Or just fill the contact form at the end of this webpage page.
In my recent work, I’ve explored two distinct approaches for multiscale modeling of an Intelligent Composite Microfiber Composite (MFC) that used piezoelectric principles. Here, a PZT sensor is mounted onto a Carbon Fiber Reinforced Polymer (CFRP) specimen, bonded by an adhesive layer to create an integrated, responsive composite system. I’ve investigated both serial and concurrent multiscale modeling techniques to understand the unique properties across different scales.
Serial Multiscale Modeling Approach
The serial method is relatively straightforward. Each scale—from macro to micro—is analyzed independently, with data transferred between scales through homogenization or Molecular Dynamics (MD) simulations. This process allows the microstructural properties to inform the macro-level response without direct real-time linkage, simplifying data management but potentially limiting fidelity in capturing simultaneous interactions.
Concurrent Multiscale Modeling Approach
Conversely, concurrent multiscale modeling presents a complex but comprehensive alternative. In this technique, data between scales—such as stress tensors—must be transferred in real-time to reflect simultaneous interactions. Based on existing literature, some methods rely on Cauchy stress tensors and other sophisticated techniques, which add complexity. For this project, I’ve implemented concurrent modeling in ABAQUS through the Submodeling technique:
- At the macroscale, the overall MFC structure is modeled, capturing global behavior.
- Moving to the mesoscale, I analyzed CFRP and PZT components, with CFRP as a woven structure and PZT as a cubic material.
- Microscale modeling then focuses on the unit cells of both CFRP and PZT.
Each level is linked using time-dependent boundary conditions via submodeling, with stress tensors exchanged simultaneously between scales.
Modeling of Isothermal Deformation in Metals and Alloys Using Strain-Compensated Arrhenius Models via VUHARD Subroutine in ABAQUS (Gleeble thermo-mechanical simulator”
For trainings and files, Please write me an email or reach out to me via:
Email: arsalanmuhammadahmad@yahoo.com
Whatsaap# +92-315-9779633
Website# https://arsalanmaa.com/design-simulation/
Or just fill the contact form at the end of this webpage page.
Price = US$500
The study focuses on modeling the isothermal deformation behavior of metals and alloys using the strain-compensated Arrhenius constitutive model within the VUHARD subroutine in ABAQUS, based on the Gleeble thermo-mechanical simulator.
Article followed and sited in video are as under:
Title: Study on hot deformation behavior of homogenized Mg-8.5Gd-4.5Y-0.8Zn-0.4Zr alloy using a combination of strain-compensated Arrhenius constitutive model and finite element simulation method
Doi# https://doi.org/10.1016/j.jma.2021.07.008
Title: Modeling and application of constitutive model considering the compensation of strain during hot deformation
Doi# https://doi.org/10.1016/j.jallcom.2016.04.153
What this model can do?
- Prediction of Flow Stress: The strain-compensated Arrhenius model allows for precise prediction of flow stress during hot deformation by considering the effects of strain, strain rate, and temperature simultaneously. This flow stress predictions allow manufacturers can adjust to adjust process parameter for the control of deformation processes such as forging, rolling, and extrusion.
- Dynamic Recrystallization (DRX) Modeling: The model integrates DRX kinetics, providing insights into microstructural evolution during deformation. This is critical for understanding grain refinement and mechanical properties enhancement during processes
- Numerical modelling: By incorporating the model into the ABAQUS VUHARD subroutine, it enables high-fidelity FEM simulations of complex deformation processes. This includes predicting temperature fields, stress distributions, and plastic strain, which are essential for optimizing industrial forming processes.
This strain-compensated Arrhenius model, implemented via the VUHARD subroutine in ABAQUS and validated through Gleeble simulations, represents a powerful tool for advancing the understanding and application of metal and alloy deformation processes.
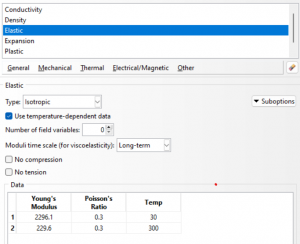
Assessing fatigue life of 3D printed biodegradable PLA specimen vs Standard PLA Specimen
In this study we have compared the fatigue life of Additive manufactured Poly lactic acid PLA specimen vs the standard specimen using a standard pull out test as a load case history for fatigue. PLA is a biodegradable, absorbable and biocompatible thermoplastic aliphatic polyester that is widely used for rapid prototyping, to manufacture tools, jigs, and fixtures designed to maximize the production efficiency, and to make biomedical components with complex shape[1]. PLA is modelled as an elasto plastic material with yielding strength of 56 MPA and ultimate tensile strength of 58 MPA due to...
Digital Healing : Numerical Simulation of 3D Printed Magnesium Bone Scaffolds for Regeneration via LDED Printing Technology
For trainings and files, Please write me an email or reach out to me via:
Email: arsalanmuhammadahmad@yahoo.com
Whatsaap# +92-315-9779633
Website# https://arsalanmaa.com/design-simulation/
Or just fill the contact form at the end of this webpage page.
Price = US$300
Hy This is Arsalan and I am back with my new project related to 3D printing in the field of biomedical engineering. Today, I will show you the details of bone scaffolds and their 3D printing, with a special focus on a magnesium-based scaffold. We’ll explore the crucial role bone scaffolds play in regenerative medicine and how 3D printing technology is revolutionizing the field. Bone scaffolds act as a support structure for bone regeneration, providing a framework for new tissue growth. 3D printing technology allows for the creation of highly customized scaffolds, tailored to the unique anatomy of each patient. This personalized approach enhances the effectiveness of the scaffold in promoting bone healing.”
Now, let’s take a closer look at the modeling process. Our journey begins with 3D modeling using Abaqus, a powerful finite element analysis software. The STL file of our magnesium bone scaffold was generated using Workbench, ensuring precision in the representation of the scaffold’s geometry. Next in line was the generation of G-codes, the instructions that guide the 3D printer in creating the physical scaffold. ReplicatorG software was employed for this task. The G-codes, which serve as the machine language for 3D printing, were then further refined using a Python script, leveraging the capabilities of the AM (Additive Manufacturing) plugin module in Abaqus. With the groundwork laid, we proceeded to simulate the 3D printing process using Abaqus. Our focus was on LDED (Layer Deposition and Extrusion Deposition) 3D printing technology, ensuring accurate representation of each layer of the scaffold. This simulation provides insights into the structural integrity, thermal aspects, and overall behavior during the printing process.”
Stay tuned for more updates on the exciting intersection of technology and healthcare.
Modeling Helical Pile Driving and Installation in Hypoplastic Clay Soil with Stiffness Anisotropy Incorporation for Cyclic and Axial Loading using VUMAT and VSDVINI via CEL approach
For trainings and files, Please write me an email or reach out to me via:
Email: arsalanmuhammadahmad@yahoo.com
Whatsaap# +92-315-9779633
Website# https://arsalanmaa.com/design-simulation/
Or just fill the contact form at the end of this webpage page.
Price = US$210
The subroutine code used here (with minor modification) is available openly for download at www.soilmodel.com. If you use this subroutine and this work than Please cite the following work of Dr. David Masin :
Article #1 “”A hypoplastic constitutive model for clays”” Doi# https://doi.org/10.1002/nag.416
Article #2 “”Cyclic lateral response and failure mechanisms of semi-rigid pile in soft clay: centrifuge tests and numerical modelling””Doi# https://doi.org/10.1139/cgj-2016-0356
Hypoplasticity is a different way to describe how certain materials, especially geomaterials like soils, behave under stress and strain. Unlike traditional Elasto-plastic models, which use concepts like yield surfaces, flow rules, and consistency conditions to describe deformation, Hypoplasticity takes a different approach. The key concept in Hypoplasticity is the idea of asymptotic states, which refers to the stable, final conditions that the material reaches under certain stress and strain conditions. By focusing on this, Hypoplasticity aims to provide a more accurate and comprehensive way of describing how geomaterials deform, without relying on the traditional Elasto-plastic framework.
In this study, the driving of a helical pile in clay soil in undrained condition is modeled using the CEL approach in ABAQUS. The initial condition in the form of void ratio/OCR and intergranular strain is initiated using the VSDVINI subroutine. This subroutine is available in Abaqus 2022 and the latest version. In the second stage of the study, the pile installation is modeled using the UMAT subroutine under cyclic loading.
In the model, you will be able to understand:
Installation of the pile in Hypoplastic clay soil under single and variable void ratio (multilayer condition) using UMAT and SDVINI.
Calculating pore water pressure and effective stress (UMAT and VUMAT).
Calculating the effective stress under axial and cyclic loading (UMAT and VUMAT).”
Comparative analysis of Mg “magnesium” Scaffold Shapes: Modelling Corrosion and Mechanical Resilience in Simulated Body Fluids”
For trainings and files, Please write me an email or reach out to me via:
Email: arsalanmuhammadahmad@yahoo.com
Whatsaap# +92-315-9779633
Website# https://arsalanmaa.com/design-simulation/
Or just fill the contact form at the end of this webpage page.
Price = US$250
Magnesium (Mg) scaffolds are biodegradable structures used in bone repair and regeneration. They mimic bone’s mechanical properties, gradually dissolve in the body, and promote bone growth through their porous design and the release of biologically beneficial magnesium ions.
A finite element-based simulation approach was used to model the corrosion and mechanical characteristics of biodegradable magnesium (Mg) scaffolds featuring diverse shapes such as Gyroid, TPMS, and BCC lattice structures. Corrosion behavior was simulated using a diffusion-driven model based on Fick’s law, capturing fluid diffusion within the scaffold to model pitting corrosion based on the corrosion rate and localization degree. To address the surface-based nature of corrosion, a Weibull distribution function was employed to apply flux at the outer nodes. A Python code was developed to create node sets on the scaffold’s outer surface and allocate flux through the Weibull distribution at each node. Each node in the scaffold initially received a concentration correlating with the magnesium’s starting concentration. Elements with Mg concentrations falling below a defined threshold (indicative of Mg(OH)2 formation) post-corrosion simulation were removed for subsequent mechanical simulations. In these simulations, Mg was considered as an isotropic, elastic-perfectly plastic material, introducing fracture via a ductile failure model. Consequently, this simulation approach effectively evaluates the influence of corrosion on the mechanical behavior of biodegradable scaffolds—a crucial aspect in designing such scaffolds for biomedical applications. This approach draws inspiration from the research article by Mohammad Marvi-Mashhadi and Wahaaj Ali, etal. titled ‘Simulation of corrosion and mechanical degradation of additively manufactured Mg scaffolds in simulated body fluid’.
This model will cover Following topics:
- How to model the corrosion in Bone scaffold as a function of fluid diffusion.
- How to modelling pitting corrosion based on varying corrosion rate
- Comparison of mechanical response of Degraded and normal scaffold specimen.
- Modelling degradation as a function of fluid diffusion time
- Python scripting to model the isotropic diffusion is simulated body fluid environment.
Chin, Cheek, and Jaw Reshaping: Using FEA Approach in Facial Enhancement for Biomedical application””
For trainings and files, Please write me an email or reach out to me via:
Email: arsalanmuhammadahmad@yahoo.com
Whatsaap# +92-315-9779633
Website# https://arsalanmaa.com/design-simulation/
Or just fill the contact form at the end of this webpage page.
🔬👨🔬👩🔬 “In our research, we have employed advanced Finite Element Analysis (FEA) techniques using Abaqus software to simulate and analyze the outcomes of chin, cheek, and jaw reshaping procedures prior to surgery. 🖥️💡 By creating digital models of the human face and incorporating the planned surgical changes, we offer a glimpse into how individuals will appear post-operation. 🌟👃 This pioneering approach not only provides patients with a visual representation of their potential aesthetic outcomes but also offers valuable insights for surgeons and biomedical practitioners. 💼📊 Such simulations can be instrumental in fostering informed decision-making for patients, reducing post-surgery dissatisfaction, and minimizing the risk of unforeseen complications. 🚀🏥 Furthermore, our work has significant implications in the field of biomedical applications, facilitating precise surgical planning and enhancing the overall quality of facial enhancement procedures. 👩⚕️👨⚕️ Ultimately, this technology has the potential to empower individuals by allowing them to actively participate in their aesthetic journey while promoting safer and more effective medical practices. 💪🌆”
Assessing Heat Generation and Thermal Fatigue based on temprature dependent S-N curve in Electric Vehicle Batteries with Different C-Ratings
For trainings and files, Please write me an email or reach out to me via:
Email: arsalanmuhammadahmad@yahoo.com
Whatsaap# +92-315-9779633
Or just fill the contact form at the end of this page.
Price ; US$120
In the pursuit of more efficient and powerful electric vehicles, understanding the intricate relationship between battery performance and thermal dynamics has become paramount. The project, “Assessing Heat Generation and Resulting Thermal Fatigue based on S-N Curve for Electric Vehicle Batteries with Different C-Ratings,” delves into this crucial junction. By subjecting electric vehicle batteries to varying charge and discharge rates, represented by different C-ratings, researchers aim to quantify the resultant heat generation. This heat, often a consequence of internal resistance and inefficiencies, can profoundly influence battery longevity and safety. Moreover, the project extends its investigation to the realm of thermal fatigue, a phenomenon characterized by the stresses endured due to cyclic temperature changes. Drawing parallels with the S-N curve used to depict material fatigue, the project seeks to develop a comprehensive understanding of how thermal fluctuations impact battery performance over time. Such insights hold the key to designing battery systems that can withstand the rigorous demands of electric vehicle operation. Ultimately, this Endeavor aspires to enhance both the efficiency and durability of electric vehicle batteries, contributing to the advancement of sustainable transportation solutions
In this project I will be covering following topics:
- Investigate the trade-offs between fast charging and battery longevity in terms of heat generation.
- Analyze the impact of different cell chemistries on battery heat dissipation.
- Investigate the impact of battery C-ratings on drawn current.
- Calculate volumetric heat generation and temperature gradient in EV batteries.
- Examine whether high C-ratings lead to thermal fatigue in batteries.
- Analyze the effects of varying conduction rates on heat transfer.
- Explore methods for maintaining batteries at standard temperatures.
- Analyze the role of thermal management systems in EV battery performance.
- Explore the impact of different charging algorithms on battery temperature.
Advancing Degradation Modeling in Biodegradable PLA bone plates and vascular Implants with Abaqus using VUSDFLD subroutine
For trainings and files, Please write me an email or reach out to me via:
Email: arsalanmuhammadahmad@yahoo.com
Whatsaap# +92-315-9779633
Or just fill the contact form at the end of this page.
Price ; US$120
Hey there, curious minds! Are you ready to embark on a journey into the world of degradation modeling? Brace yourself as we dive deep into the fascinating realm of biodegradable implants. In this captivating video, I’ll unveil the secrets of modeling degradation in Biodegradable Vascular Stents and Bone Plates, using the incredible Abaqus software via VUSDFLD subroutine. Prepare to be amazed! 👨🔬💻
Our Elasto-plastic material model captures the properties of bone plates, stents, and bones, while a hyperplastic model replicates vessel behavior. With the implementation of VUSDFLD, we calculate degradation based on time and strain, guiding our understanding of the implants’ performance. ⏳📊
Fracture initiation in PLLA stents is determined by the element death criteria, ensuring accurate simulation. The element death criteria is as under “”. Once the maximum principal strain decreased to lower than the fracture strain, the fracture will be initiated in the PLA. This approach provides valuable insights into the implants’ fracture behavior and aids design optimization. 💥🔍
Benefit of the tutorial:
- Gain comprehensive insights into the behavior of biodegradable implants through step-by-step tutorials.
- Learn to model Biodegradable Vascular Stents, including the crimping, expansion, and relaxation phases.
- Master the art of writing a VUSDFLD code that accurately predicts degradation in any biomedical implant.
- Explore the modeling of biodegradable bone plates attached to healing bone sites.
- Understand degradation modeling with respect to time and strain, enabling precise analysis of implant performance.
- Calculate degradation degrees as a function of time, empowering a thorough understanding of implant degradation. ⏳📊
Modelling of Fiber metal laminate(Aluminum + GFRP) using Abaqus via VUMAT and Ductile Damage Criteria
For trainings and files, Please write me an email or reach out to me via:
Email: arsalanmuhammadahmad@yahoo.com
Whatsaap# +92-315-9779633
Or just fill the contact form at the end of this page.
Price ; US$100
Hey there! Are you interested in learning how to create the perfect Fiber metal laminate composite? Well, you’re in luck! In this video, I’m going to show you how to model and test FML composites for Aluminium and GFRP material under tensile testing.
The model use the Subroutine code VUMAT based on Hashin’s instant damage criteria to model the GFRP While ductile damage criteria is used to model the Aluminium. The GFRP is tested with various lay stacking sequence and the damage extent for differnt lay up orientation i.e. 0° and 90° and is evaluated.
Numerical Modelling of drilling operation in reinforced concrete Slab using ABAQUS
For trainings and files, Please write me an email or reach out to me via:
Email: arsalanmuhammadahmad@yahoo.com
Whatsaap# +92-315-9779633
Or just fill the contact form at the end of this page.
Price ; US$70
Have you ever wondered what goes into drilling a hole into a reinforced concrete slab? As a simulation FEA engineer, I’m here to take you through the process using ABAQUS software. In this video, we’ll be using the CDP material model for concrete and ductile damage for reinforcement to simulate the drilling operation in a reinforced concrete slab. Let’s dive in By using advanced simulation techniques, we can model the behavior of the slab as it’s drilled into. The CDP material model for concrete allows us to accurately capture the cracking and failure of the material, while the ductile damage model for reinforcement lets us simulate the damage and deformation of the steel bars. By running these simulations, we can predict the behavior of the concrete slab under various drilling conditions, and optimize the drilling process for maximum efficiency and safety.
Modelling air blast and surface explosion (TNT) in reinforced concrete bridges using ABAQUS.
For trainings and files, Please write me an email or reach out to me via
Email: arsalanmuhammadahmad@yahoo.com
Whatsaap# +92-315-9779633
Price# US$120
Or just fill the contact form at the end of this page.
This model provides requirements for the design and construction of reinforced concrete structures, including those subjected to blast loading as per American Concrete Institute (ACI) 318 Building Code and International building code (IBC).
The Concrete Damage Plasticity model is used to simulate the non-linear behavior of concrete materials, taking into account the damage caused by tensile and compressive stresses. On the other hand, the Ductile Damage Criteria is used to simulate the behavior of steel reinforcement under extreme loading conditions, taking into account the damage caused by the rupture of steel bars.
The simulation of the 50 kg TNT explosion on the surface and in the air is important to understand the effect of blast loading on reinforced concrete bridges, which are critical infrastructure elements. The results of this study can provide insights into how reinforced concrete bridges behave under extreme loading conditions and can help engineers and designers to develop more robust and resilient bridge designs.!
Modelling deformation and crack propagation in MMC under compressive load using DIGIMAT and ABAQUS
For trainings and files, Please write me an email or reach out to me via
Email: arsalanmuhammadahmad@yahoo.com
Whatsaap# +92-315-9779633
Or just fill the contact form at the end of this page.
This is an advanced training course designed for engineers and researchers who want to learn deformation behavior of metal matrix composites (MMCs) under compressive loads. This course covers the use of two powerful simulation tools, DIGIMAT and Abaqus, to model the compressive behavior and crack propagation in MMCs. The first part of the course provides an overview of metal matrix composites and their applications. It covers the basic properties of MMCs and the factors that affect their behavior under compressive loads. The damage model for Aluminum and the reinforcement is calculated and explained using excel sheet. The second part of the course focuses on the use of DIGIMAT, a specialized software for modeling the mechanical behavior of composite materials. Participants will learn how to use DIGIMAT to create the 3D geometry of MMC using volumetric combination of 90%AL-10%Ti3alc2 The third part of the course focuses on the use of Abaqus, a powerful finite element analysis software. Participants will learn how to use Abaqus to create finite element models of MMCs under compressive loads. They will also learn how to simulate crack propagation in MMCs using Abaqus. Throughout the course, participants will work on hands-on exercises that will help them develop their skills in modeling the behavior of MMCs under compressive loads. By the end of the course, participants will have a solid understanding of the behavior of MMCs under compressive loads and the skills needed to model this behavior using DIGIMAT and Abaqus. If you are an engineer or researcher who wants to gain a deeper understanding of the behavior of MMCs under compressive loads and the skills needed to model this behavior, then this course is for you!
Analyzing damage in multilayer CFRP-GFRP woven composite using Abaqus
For CAE files and tutorial, Please write me an email or reach out to me via WhatsApp
CFRP (Carbon Fiber Reinforced Polymer) and GFRP (Glass Fiber Reinforced Polymer) are composites that are used in a variety of applications. These composites are made by combining a polymer matrix (typically a resin) with fibers (carbon or glass) to create a material with improved properties compared to the individual components. CFRP composites are known for their high strength-to-weight ratio, making them ideal for applications where weight savings are important, such as in aerospace and automotive industries. The carbon fibers used in CFRP composites also provide excellent stiffness and resistance to fatigue and creep, making them ideal for structural applications. GFRP composites, on the other hand, are more widely available and less expensive than CFRP composites. GFRP composites are known for their high resistance to corrosion and are often used in applications where durability and long-term performance are important, such as in construction, civil engineering, and water treatment.
Woven composites refer to composites where the fibers are woven into a fabric-like structure. This type of composite provides improved mechanical performance compared to non-woven composites, as the fibers are able to interact with each other in a more organized and controlled manner. Woven CFRP and GFRP composites are often used in high-performance applications where the combination of high strength and stiffness is important.
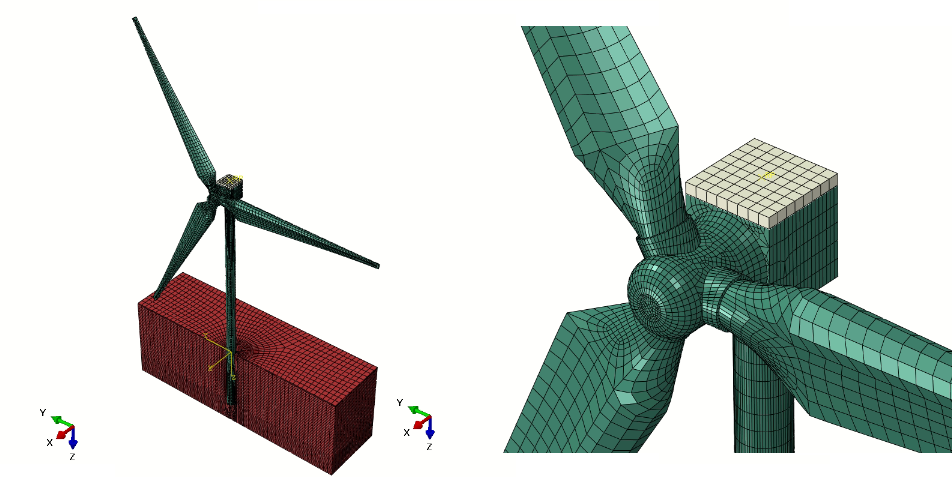
Assessing cyclic response of the wind mill using hypoplastic clay model .
Hypoplastic constitute law is best choice to predict the non linear behavior of the soil. Hypoplastic constitutive laws are used to describe the deformation behavior of the granular soil and clay at a given strain rates. In constitutive law the soil deformation behavior is explained in term of soil stress and strain rate in which stress and strain rates are regarded as function of time[1]. In case of soil the stress tensor is not only a function of strain as in case of elasto plastic material but instead complete deformation history is required to predict the behavior of the soil [2]. In...
No Results Found
The page you requested could not be found. Try refining your search, or use the navigation above to locate the post.
No Results Found
The page you requested could not be found. Try refining your search, or use the navigation above to locate the post.
Additive manufacturin of Airless tyres using Viscoelastic model based on polymer extrusion technique
In FEA basic aim of 3d printing simulation is to predict thhe excessive distortion and residual stresses during rapid heating and cooling of the part during printing. The airless design taken in this study is from Bridgestone tyres. This airless tire technology features a unique spoke structure designed to support the weight of a vehicle, effectively eliminating the need to periodically refill the tires with air.
Additive Manufacturing (AM) is an appropriate name to
describe the technologies that build 3D objects by adding
layer-upon-layer of material. In this simulati0n progressive material addition based on polymer extrusion technique is used to deposit layer of material. In Polymer extrusion technique an extruder puts down molten beads on top of a previous layer and as they solidify, they fuse to the
existing part
Abaqus Modelling
A coupled thermo-mechanical simulation is performed in abaqus using Polyurea as a base material. First, a heat transfer analysis is performed on the part with appropriate and specific temperature boundary conditions and flux
loads(laser) Once the heat transfer analysis is complete, the temperature profiles are used to drive a static analysis of the part to predict distortions. Position and time of the laser is specified by entreing event series data that comes from the NC codes generated by convential softwares Replicator/creo-CAM. Also from the stres analysis of the tyre for the exisitng material model it was observed that these tyres can easy withstand load of 700-1000kg with deformed excessively.
Modelling High cycle Fatigue and assessing failure probability for reinfoced concrete bridges using site specific fatigue load model
This model analyzes the fatigue failure of low strength reinforced concrete bridges using a site-specific fatigue model. Since AASHTO truck does not reflect the extent of damage caused by actual traffic load traversing a bridge, a new fatigue load model has been proposed on the concept of equivalent damage using Miner hypothesis. Thus incorporating an axle width and the distance between the tyres, a single axle load of 210 KN was considered in the model. The outcomes of this model are vital in term of in identifying the severity of Fatigue Damage
Abaqus Modelling
A low strength concrete mode with maximum compression strength of 16 MPa is used in material modelling. Moving load was applied using a user subroutine VDLOAD. This subroutine enabled us to define the magnitude of wheel load as a function of position, time and velocity. From the stress profile at the most critical node at the mid span section of the bridge, It was analyzed that the stress generated due to self-weigh is 147 MPa and this stress start increasing gradually as the fatigue load travel toward mid span of the bridge. This peak value of the stress which is below the yielding limit of the steel is used further in FE-SAFE for calculating the Fatigue failure life cycle.
Fe-SAFE
After importing the results in fatigue, S-N curve of the material is specified and Un-axial stress life approach is used as a fatigue evaluating criteria. Profile of the passing truck is specified in the amplitude section which estimates the fatigue failure cycle equal to 4.09 million trucks. In the next section the performance of structure is assessed by monitoring its failure probability under different load variance percentage. This is performed by defining Weibull distribution to the material strength (S-N Curve). From the results as in Figures it was analyzed that at early stages of fatigue life, the reliability of the bridge with high load variation is low.
Modeling & predicting fatigue life for silicone(H-elastic) PIP finger implant using Abaqus & Fe-safe
Proximal interphalangeal (PIP) joint replacements have been performed for many decades with silicone implants with substantial acceptable to good outcomes. The PIP joint links the first and second phalanges of the finger. The aim of the study is to to improve the functional range of finger motion among individuals with posttraumatic degenerative changes in PIP joints. In this study an hyperelastic material model based approach is used to model the behaviors of PIP implant with different degree of flexion and extension. As these type of implant are mainly designed for flexion case, the range of flexion motion is then analyzed furthering Fe –safe for predicting fatigue strength. The Ogden hyperelastic material model based on three coefficients is used both is Abaqus and Fe-safe. Results shows that fatigue life is directly affected by range of motion with Fatigue life ranging from few thousand cycles for high degree of flexion to millions for small degree of flexion mainly 10 and 20 degree.
Predicting worst cycle repeats/hours for hyperplastic brake pads used in conventional band brakes.
Band brakes operated by pressing a thin layer of brake pads against a rotating drum. This results in generating a frictional force that results in deacceleration of drum. The frictional force generate heat that adversely effect the performance of the braking pads which results in wearing of the pads. Thus fatigue performance of braking pads is effect by combined response of temperature and mechanical pressing. Hyperplastic material model based on reduced polynomial is used to model the braking pads. While the results from Abaqus is exported to Fe-safe and worst life cycle is approximated using Rainflow cycle counting algorithm. Results shows that with a by applying extreme mechanical displacement force that worst cycle is 578 hours.
3D Bio-printing of full size model of Humun heart
Motivated by the study of Eman Mirdamadi conducted at University of Maryland in which they have used Freeform Reversible Embedding of Suspended Hydrogels (FRESH) bio-printing of a complete humun heart using alginate as the printing biomaterial to mimic the elastic modulus of cardiac tissue. In this model a numerical based study is conducted for modelling of 3D printed humun heart using properties that mimics soft tissue of humun heart. The temperature is kept as low as room temperature as humun tissue cannot sustained high temperature. The whole model is carried out in #abaqus, thanks Dassault Systèmes for such an amazing software solution that will hopefully revolutionize Bio -artificial organ manufacturing
Modelling Probability of survival of welded Pipeline X-joint using S-N curve; High cycle fatigue case
The study aims to assess the integrity of welded X joint under thermal load. The welding of the joint is carried out using DFLUX subroutine. The stress increment corresponds to end of the welding is imported into FE-SAFE. FE-safe is a software by DASSAUL SYSTEM used for assessing fatigue reliability of the structure. Afterward, the probability of the welded joint is analyzed for different load variance. Result shows that for high load, at later stage the probability is low as compare to early stage which depicts the fatigue reliability of structure.
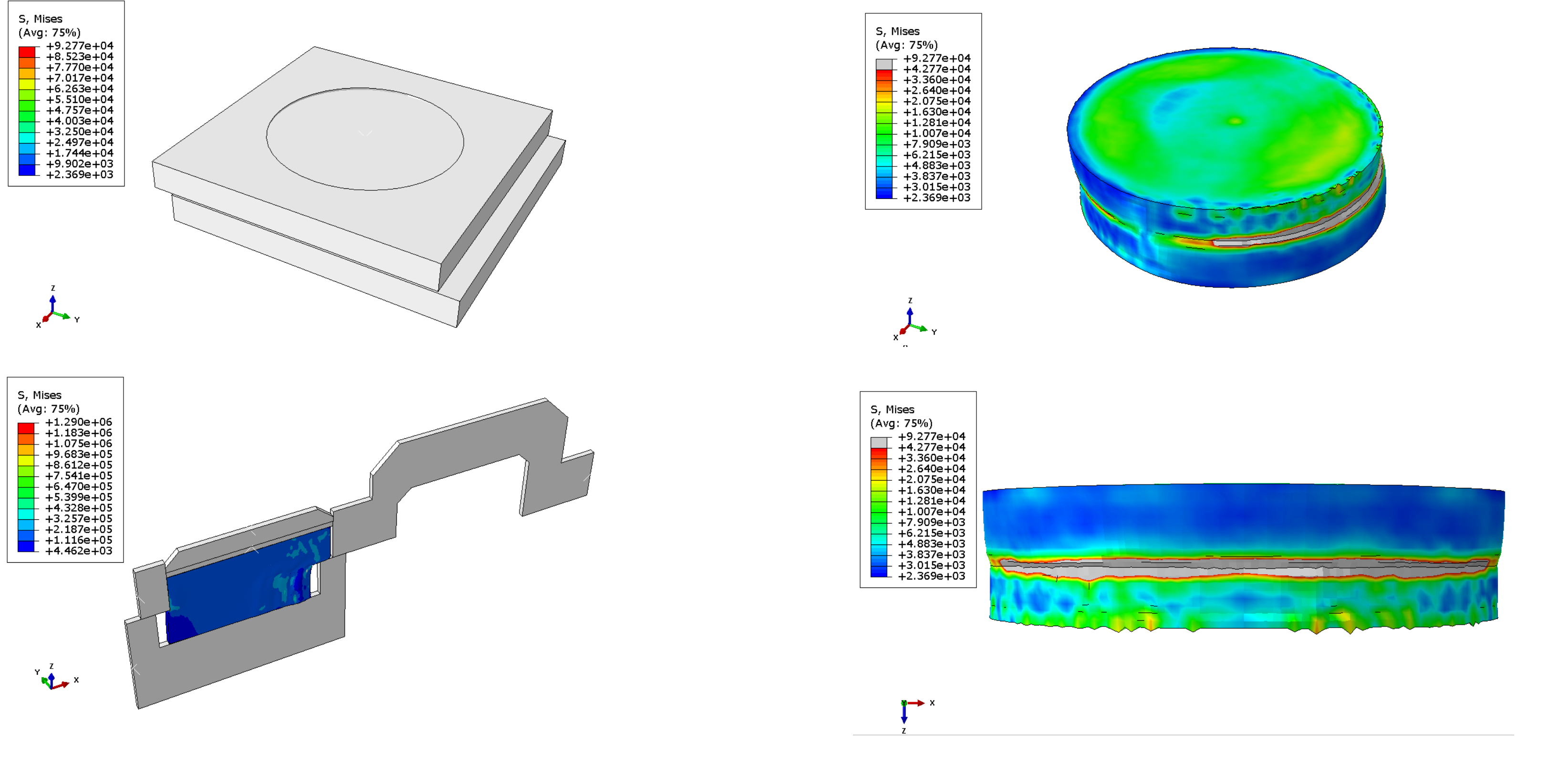
Modelling Direct shear and modified direct shear test 5of clay soil USING CEL approach in ABAQUS
The study aims to model the direct shear test using CEL APPROACH IN ABAQUS. Direct shear test apparatus is used to determine residual shear strength of the soil. In order to accommodate large strain behavior, coupled Eulerian Langragian Approach is used to simulate DS approach. Clay soil with a cohesion of 0.03Mpa is used to simulate the shearing behaviour while a displacement of 10 mm is applied to the bottom box. Both boxes were kept one above each other with a gap of 1mm. The maximum shearing force for the soil measure at 20KN WITH A DISPALCMENT OF 10mm.
Durability analysis of buried pipelines crossing under railway track; High cycle fatigue case(Fe-safe & Abaqus)
The study aims to assess the integrity of buried oil and gas pipelines crossing railroad impacted by moving train. A user subroutine VDLOAD is used to model the wheel load on the multilayered soil structure while railway sleepers were modelled using a high strength concrete. For analysis purpose ABAQUS is used to model the dynamic behavior of the moving train load while Fe-safe which is produce of Dassault system is used to predict the high cycle fatigue by estimating the failure cycles as well reliability of the pipeline structure under different load variance. Different diameters pipelines were arranged at different depth in the soil structure lying perpendicular and parallel to direction of moving load. Results shows that pipeline lying parallel to the direction of the moving load experience more impact and hence fatigue failure at the circumference of the pipeline in expected more severely.
.
Modelling highly energy absorbing Polyurea-GFRP composite for resisting bullet impact using VUMAT-VUSDFLD subroutine
The study aims the perforation resistance of the PU-GFRP composite under high velocity impact. Polyurea is modelled as a visco-elastic material model with a strain rate of over 50,000s-1. At this strain rate the material behave as a glass transition material with failure strain of 0.2. The damage in elastomer is modelled using maximum failure strain criteria. GFRP is modelled using Hashin damage criteria with layer thickness of 0.3mm oriented at 0 degree. Results shows that model is capable of stopping bullet travel at over 1500km/hr.
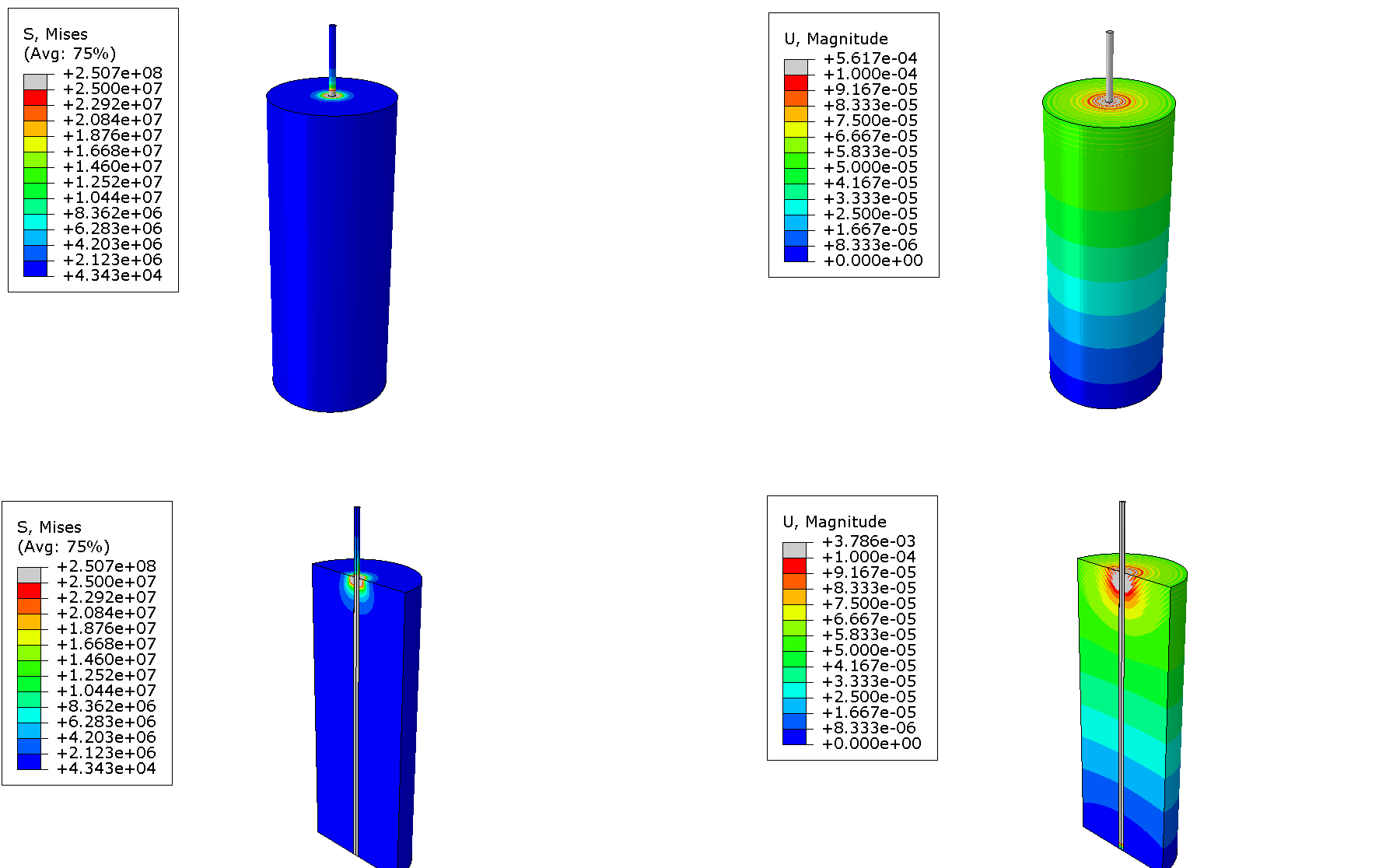
Modelling creep relaxation in CFRP embedded concrete incorporating the cohesive bond slip behavior
The study aims to analyze the creep relaxation of concrete cylinder with embedded CFRP bar. A standard pull out test is modelled and time-dependent behaviour of concrete is taken into account in a visco-elastic analysis using the creep laws given in Eurocode 2. The CFRP bar are prestressed and decrease in prestressed is simulation alongside its evolution. The stress state reproduced inside the concrete and its evolution correctly matched with the various experimental studies found in the literature. From the result it is concluded that the due to slip restriction greater stiffness is found in the unloading step as compared to the loading step.
Modelling drilling and settlement of helical pile using Mohr-coulomb(VUMA) based on stress return criteria.
Conventional Mohr Coulomb model is non-trivial to implement in the finite-element method due to the fact that the Mohr-Coulomb yield criterion and the corresponding plastic potential possess corner sand an apex, which causes numerical difficulties. Mohr coulomb is limit function plot as a non-uniform hexagonal cone in a plane stress strain. The Mohr coulomb yield function has a corner which may cause difficulties while may cause difficult in the modelling complex finite element analysis scenario. ABAQUS built in model uses a rounded version of plastic material which may not run stable for perfectly elastic material. In this model stress update criteria is used with small modification to the formulation of constitutive matrix on corner and apex is performed. A 3d helical pile installation and settlement in performed in a sandy soil with negligible cohesion, and the results shows that resultant settlement is a key function of cohesion as well as loading rate
Modelling incremental hole drilling for residual stress analysis of AA7050-t7451 specimen
Incremental hole drilling is widely used technique to measure the surface residual stresses due to its high precision and being economic. In Incremental hole drilling process, a rosette is installed having capability of measuring multi directional strain, a hole is drilled in the center through a successive increments and surface stress stresses are monitored. This incremental hole drilling methodology converts the relaxed strain induced by the hole drilling into a sub-surface stresses which is the measured by the installed rosette gauge. Experimentally at the position of the hole drilling, a rosette with 3 different gauges arranged at 00, 450 and 90. Stress maximum when the angle of applied load is parallel to direction of stress measurement. While it is found to be almost negligible for the other 2 orientations
Concrete crack detection using piezoelectric sensors based on time reversal method
Time reversal approach has been widely utilized as an efficient damage detection tool. Structural damage, such as crack and delamination, generates nonlinearities that break down the signal reconstruction characteristic of time reversal method. As a result, the difference between the original input signal and the reconstructed signal shows damage. According to the time reversal approach, an input wave signal may be rebuilt at any excitation point by reversing the output signal recorded at another point of the structure in the time domain and retransmitting it back to the excitation point.
.
Stress analysis of concrete beam reinforced with prestressed CFRP and steel tendon
The study aims to compare the performance of reinforced steel and CFRP tendons . Irrespective of high strength and ductility of prestressed steel tendons, steel tendons are avoided due to high susceptibility to corrosion. The corrosion of the prestressing steel reduces load carrying capacity of the prestressed member and result in catastrophic failures. Carbon Fiber Reinforced Polymer (CFRP) have been implemented in concrete structures as a solution to this problem. However, concrete beams prestressed with FRP tendons have showed brittle flexural failure due to the elastic rupture of FRP tendons.
.
Comparison of Kinematic hardening vs isotropic hardening plasticity model for low cycle fatigue case
The study aims to analyze the behavior of pipe bends under constant cyclic loading case. Two advanced plasticity model were adopted in the study based on von mises yield surface. The first model adopts Armstrong-Frederick (AF) non-linear kinematic hardening model based on center and size of the yield surface. The size of the yield surface is assumed to be constant. The Isotropic hardening plasticity law is implemented using UMAT based on power hardening rule based on yield condition and plastic flow rule. From the results it was concluded that the A-F kinematic hardening law can accurately predict the cyclic response for joints as compared to the isotropic hardening rule.
.
Simulation of CFRP/GFRP woven composite structure under high velocity bullet impact using VUMAT (Abaqus+ DIGMAT)
The aim of the project is to assess the impact of bullet on the woven composite. VUMAT based on Hashin damage criteria is implemented for CFRP and GFRP composites. Stress wave propagated fast in the direction perpendicular to the direction of fibers. A cohesive contact model based on the traction separation law is implemented on the interface between CFRP and GFRP woven composite.
.
Modelling movement of F-16 fighting aircraft in airstream
The study aims to analyze the mechanism of air flow around the flying F-16 aircraft. These parameter involve analyzing 3d air vector field around each individual component of aircraft. Also the formation of fluid vortices around the aircraft is analyzed. The maximum force applied by the airstream moving with speed of 40m/s exerts maximum force of 200kN.
.
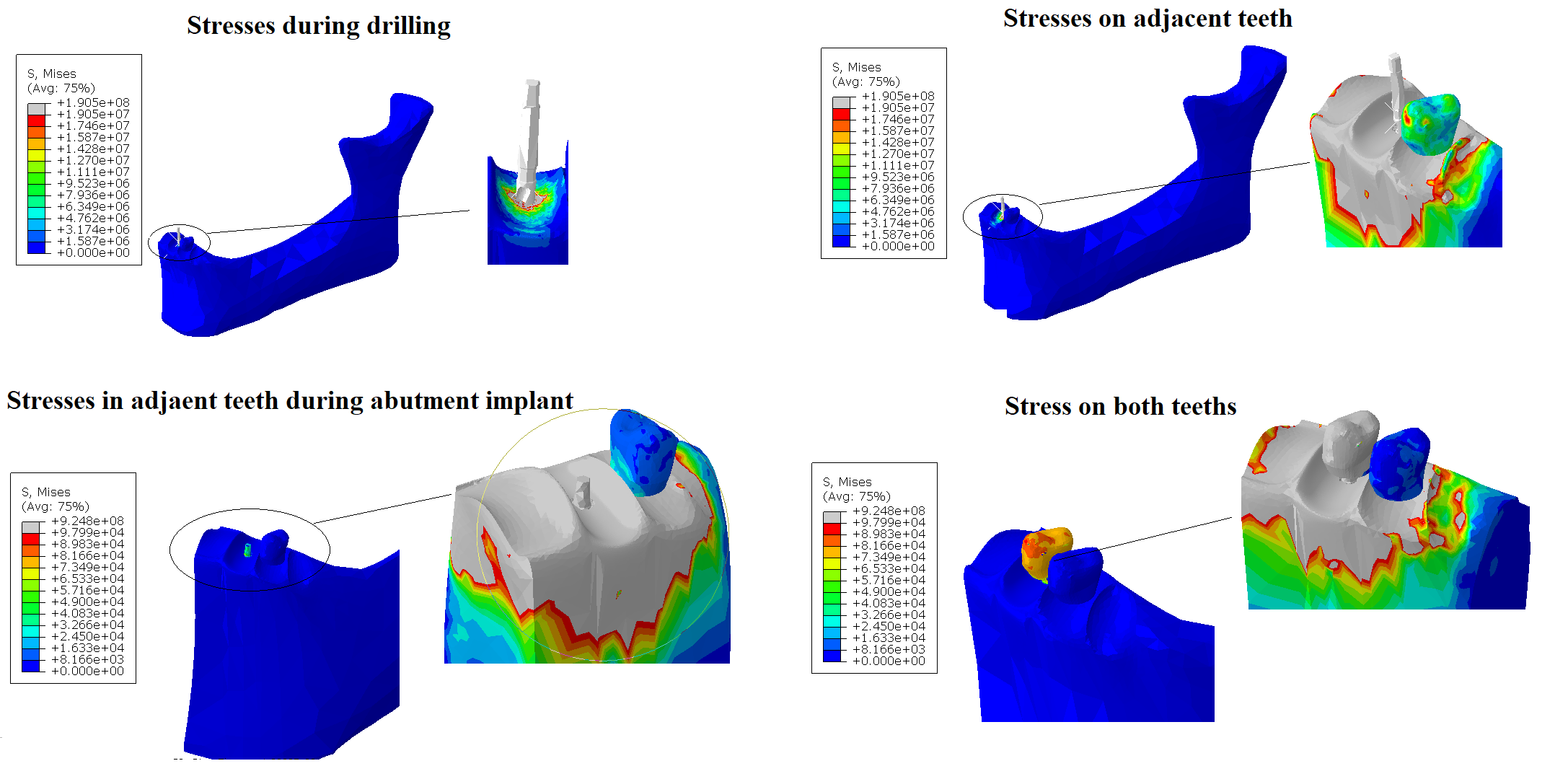
Modelling effect of Titanium/gold implants on the adjacent teeth
The study aims to assess the effect of the titanium and gold alloy implant on the adjacent teeth. Dental implant involves complex drilling process which induce stresses on the adjacent teeth. Quantification of these stresses contribute toward assessing the integrity of adjacent teeth during the implant process. Result shows that peak stresses induced in the root of adjacent teeth were almost 90% high for the gold alloy implant as compared to titanium implant.
.
Analyzing knee compartment load for arthritic patient under variable midsole wedge angle
In this study, knee compartment stresses were analyzed under variable midsole wedge angle. For each of wedge angle, two different coefficient of friction values were considered , one for the healthy and one for the arthritic patient.
Results shows that the stresses at the bone interface is directly influenced by the coefficient of friction while if we reduce the midsole wedge angle along the Center of pressure of the interacting bones, than it can reduce the stress at the knee interface. As in our case reducing the angle by 50% cause 24.3% reduction in medial compartment stresses, in turn providing significant releif to arthritic patient.
.
To study the aerodynamic performance of the rotating wind turbine
The study aims to assess the effect of the performance of the rotating wind turbine under mild air flow rate.
This aerodynamic model includes static pressure effect, vorticity and resulting of forces generated on the blades under air velocity of 10m/s.
.
Modelling High cycle fatigue for underground Pipeline using S-N curve method
The purpose of the study is to calculate the high cycle fatigue for buried pipeline using conventional S-N curve method.
Different Fatigue damage model based on Biaxial and uniaxial stress criteria were used to to predict the fatigue life while Rain flow cycle counting algorithm is used to to determine the fatigue cycles. Different fatigue parameters i.e. Fatigue fracture strength, fatigue strength coefficient, Coffin-Manson exponent, cyclic elastic modulus.
.
Modelling installation of helical pile in a hypoplastic sand using VUMAT
A hypoplastic constitutive model
is used to match the soils behavior realistically
The model by Von Wolffersdorff (1996) is considered as a reference model for predicting the soil hypoplastic response. This model take into account parameters like critical friction state angle, granular hardness, minimum, maximum and critical void ratio, stiffness ration. The installation process is simulated using coupled Eulerian Langragian CEL approach. The reaction force of the surrounding soil is investigated. Soil nearby displacements as well as effect of the changing stress state and the bulk density is analyzed.
.
Modelling stretching of a polychloroprene rubber using Subroutine UMAT,UHYPER (Mooney-Rivlin).
The study aims is to define the strain energy potential for an isotropic hyperplastic material using Mooney-Rivlin method.
The deformation gradient is then passed to UMAT for each prescribed node. The model consist of a rubber strip which act as a housing for metallic chips. The housing is covered by a rubber top which serve as a protective layer for inner material. The rotation and axial force is applied across the two extreme ends and the resulting behaviors is analyzed at the center of the strip. Al linear relationship is observed between a angular/linear deformation and the force applied at the extreme clamps.
.
Optimization of steel interlock connectors for modular buildings
The aim of optimization is reduction of material volume without compromising the stiffness of the connectors.
Design and construction of reliable interlocking system is identified as key challenge in the assessing the response of the modular buildings. Through Interlock connectors one can predict the critical load limiting capability of the modular building and thus these connection are key to the overall robustness of the structural system. In the optimization preprocessing, maximizing the stiffness by minimizing the design response value of the strain energy is taken as objective function. While volumetric reduction is considered as a constraint in the optimization task.
Modelling Plain milling for steel specimen along with formation of discontinuous chip
The total length of the specimen is 100 mm. Cumulative damage model which includes Ductile damage criteria alongside damage evolution, shear damage criteria are used to predict the damage initiation. While Johnson cook parameters are used to model its plastic behavior with damage evolution. Solution dependent variables were taken as unity. Temperature DOF were allowed at the integration points using Dynamic temperature explicit step. Formation of the chips strongly influence by the rotation speed of the tool. For the interaction the drill surface is connected with the nodes of the work piece using kinematic contact using thermal gap conductance, heat generation, and penalty as interaction property. The tool surface is coupled at the center while defining the COR at a same point while defining rigid constraint.
Modelling High cycle fatigue for an embedded reinforcement using normal strain Morrow criteria in Abaqus”FE-safe”
This aim of this model is to calculate the the failure cycle for a reinforced beam
Results from Abaqus ‘ODB’ is imported into Fe-safe. The stress tensor is then multiplied by the time history of applied loading to produce time history for each tensor. A multi axial fatigue model is use to convert elastic stress-strain history into plastic stress strain history. Individual life cycles are counted using a rain-flow cycle logarithm and total damage is summed. The element with the shortest life define the start of crack initiation.
Analyzing multi-axle dynamic load on reinforced bridge using VDLOAD subroutine.
This model aims to quantify the stresses developed on concrete and steel structure using VDLOAD subroutine.
Both front and rear tyres with width of 3mm exerts surface pressure of .5 MPa on to the concrete surface. M25 concrete parameters are used to model the concrete while high strength X70 steel is used to model the embedded reinforcement. The stresses computed will be used to estimate the integrity of the bridges under critical loading conditions.
Modelling Micro Vickers hardness test for “Al2O3“– “Ti-6Al-4V” based composite.
The model aims to calculate hardness of a composite material based on Vickers hardness principle
The tip of the indenter is a square pyramid having edge angle of 136 with the vertical plane. This indenter produced the same geometric impression upon interacting with the work piece. Based on length of the diagonals, one can calculate the hardness of the material. The test is preferred as an alternative to other hardness measuring techniques as the required calculation are independent of the size and hardness of indenter.
Variation in thickness of 304L stainless steel sheet during hydroforming Process
The project aims to measure the variation of thickness along the circumference of the steel sheet during the Hydroforming operation
It was Also concluded that the stress required to form the sheet into required can shape is as high as 1000 N/mm^2. The thickness of the sheet varies from initial values of 0.9525 mm to .20 mm.
with Simulation of Deep drilling within multilayered soil structure using couple Eulerian Lagrangian Approach
Mohr coulomb plasticity model is used to model different soil layer with cohesion strength varying from 0 to 300 kPa.
Results shows that the stresses generated within soil structure directly related with the cohesion of the underlying soil. Stress propagation is maximum in a soil with increase cohesion strenght.
Numerical analysis of live vehicular load on the buried X70 gas pipeline using Cap-plasticity model (modified Drucker–Prager model)
In the beginning of the analysis, gravity loads and instantenous load in the from of forced vertical displacment is applied to the soil layer.
Currently, X70 pipeline is widely used in Oilf and gas industry for trasnporatation of liquid fuel due to its increased resistant and corrosion resistant properties. Results shows that by imparting vertical displacment of 5 mm onto the soil layer, resulting force on the pipeline periphery is as high as 150,000N.
Numerical analysis of surface grinding operation using single and multiple grit cutters geometry
Influence of different cutter geometries on the grinding chracteristic is simulated.
Increasing number of grits in the cutter directly influence the resultant cutting force. Formation of chip is directly related with the tool rake angle and the feed rate. ALE is utilized to increase computational efficiency as well as to avoid excessive distortion of the element during high speed cutting.
Numerical analysis of the damage behaviour of the polyamide CFRP composite beam laminated with cohesive layer
Three point bending test is performed on hybrid beam using different loading condition.
For internal reinforcing layer of the beam, which dominated by fiber glass layers and the outer polyamide layer, the matrix failure index of HashinRotem’s failure criterion was chose While debonding between fibre glass and Polyamide layers was modeled by the cohesive zone model with the traction separation law using Qudratic stress damage criteria.
Modelling pull out strenght of ribbed and plain steel rebar from concrete block with account of surface based cohesive interaction in Explicit step
The model aims to analyze the shear strengh by developing a localized bond slip behavious across the component of reinforced concrete
The interface between concrete and steel is the principal cause for both the strength and the deterioration of structures. Abaqus explict cannot cannot directly incoporate the effect of cohesive damage across the the interfaace of the bond. Steel concrete bond is developed using an linear elastic traction behaviour with damage initiation and onset.
Equilibrium solution for a layer of soil loaded by a rigid, perfectly rough strip footing
The model analyze the bearing capacity of the underlying soil under rigid concrete footing loaded with external pressure.
The behavior of soil is simulated using the cam -clay model (modified Drucker–Prager model) with parameters matched to the classical Mohr– Coulomb yield model parameters c and φ. . The model provides necessary resistance during compression to the soil by bounding the yield surface thus it provides an inelastic hardening mechanism to represent plastic compaction. Also, this model control volume dilatancy when the material yields in shear by providing softening as a function of the inelastic volume.
MODELLING STEADY AND TRANSIENT HEAT TRANSFER THROUGH CEMENT KILN
Rotary kilns are an advanced thermal processing tool used for processing solid materials at extremely high temperatures.
Rotary kiln consist of brick at the internal lining, enclosed in the steel structure. Convective and radiative heat losses thought he kiln surface are often ignored.. These losses can be reduced by painting the kiln surface with a low emissivity paint. It can be estimated that that by painting the surface with a low emissivity paint the losses can be reduced to as much as much as 3 %.
Design and NC code manufacturing of V12 Engine cylinder head
V12 engine comes with classic 12 cylinder banks arranged at 60 degree and is compact- measuring 848 mm wide, 336.86mm in lenght and 351.46 mm tall.
It has a bore diameter of 120.710 mm and a cylinder stroke of 90.4 mm.. Drilling of cylinder bore is carried out at a feed rate of 100mmPM with a spindle speed of 2000rpm. Oil passages were manufactured using trajectory milling and rough milling techniques.UNCX01.P12 post-processor was used to generate G codes for manufacturing process
.
MODELLING DENTAL IMPLANT TO EVALUATE STRESS PROPAGATION ON ADJACENT TEETH
A dental implant is used to support one or more false teeth. It is a titanium screw that can replace the root of a tooth when it fails. Just like a tooth root, it is placed into the jawbone This model analyze the stress generated during various faces of the dental implant and estimate the stress distribution and its effect on the adjacent teeth.
DESIGN OF SLIDING LEVER MECHANISM FOR REDUCING EARTHQUAKE ACCELERATION IN BUILDING STRUCTURES
A new configuration consisting of a ramp lever , dampers known as “sliding lever mechanism technique” was developed, the geometry of which is arranged such that it would not increase axial or shear demand on columns yet at the same time making more space available for architectural symmetry. For this purpose, a three story experimental model was tested for Imperial Valley 1908 earthquake.
STRESS EVALUATION ON CONCRETE BEAM USING SOLID ELEMENTS
These models focuses on to estimate the load on the simply supported concrete beam. The reinforcement is model as a solid steel section in a second case. Both design lead to comparable results. also the optimization of steel reinforcement in order to attain maximum bearing strength
SIMULATION OF STATIC LOAD ON UNDERGROUND OIL AND GAS PIPELINES
These models focuses on to estimate the load on the simply supported concrete beam. The reinforcement is model as a solid steel section in a second case. Both design lead to comparable results. also the optimization of steel reinforcement in order to attain maximum bearing strength
arsalanmuhammadahmad@yahoo.com
Feel absolutely free to contact me!
Whatsapp# +92-315-9779633
Design and Simulation of various Engineering Concepts